GE dryer troubleshooting. Diagnosing and repairing the more common problems that GE dryers can be done by homeowners.
The most common problems that GE dryers are some of the same problems that plague newer models of all-electric clothes dryers.
It’s likely you already have most of the tools and test equipment you need in your DIY tool kits such as an iron and a multimeter. Before tearing into your own dryer, always check for simple problems.
Make sure that the dryer’s power cord is plugged into the wall outlet at home and that its circuit breaker on the service panel has not tripped open.
GE dryer troubleshooting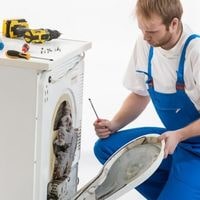
If you’re looking for help with your GE dryer, look no further. Our comprehensive troubleshooting guide will show you who to contact and what information to provide them once our experts have diagnosed the problem of your appliance.
GE Dryer Does Not Start
The first step towards solving a dryer problem is to test if the start switch could be defective.
If it’s humming, but not starting up, the problem has nothing to do with this switch.
If it doesn’t respond or make any noises, then you know for sure that something’s wrong. A multimeter can be used to test if the switch is working properly by finding out if there’s still continuity after pressing it in different positions and comparing that with a good switch’s readings.
Otherwise, you can always just replace it. The switch is held in place by two screws on each side and disconnects from the wiring harness and holds onto a wire between two pins by means of a clip.
GE Dryer Starts But Drum Does Not Turn 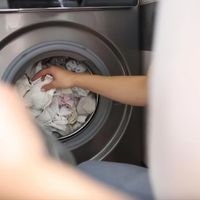
There are two types of common errors due to problems with the Dryer Drum Assembly.
One is an issue of the belt itself (less likely but still possible to happen), and the other is an issue with the idler pulley that is meant to keep tension on the dryer drum belt properly.
Being that this is mechanical in nature, it’s very likely that this could be caused by a problem with either one or both of these parts.
The belt is composed of a tightly woven fabric strip made up of multiple long strands connected end-to-end, such as a cord or wire.
The drive belt travels around the outside spur gear, then it goes underneath the plastic idler up against the back wall with this in mind usually by far causing enough friction so that even though you load it fully, when you turn on your dryer there will be no slipping or stretching of this part.
GE Dryer has stopped spinning
When your dryer is not operating as it should be, the problem may be caused by a broken drive belt.
The drive belt can cause the drum in your dryer to spin freely, which means the machine might not fully tumble and could leave clothes damp or wrinkled.
In order to determine if the belt is broken, open up your dryer door and reach inside to give the drum a few turns with your hands. If you feel that the dial spins very easily, your drive belt is likely broken.
Once you’ve figured out that this component part is indeed faulty, check for cracks or other abnormal signs of damage on its surface. Next, take off the old drive belt and replace it with a new one to speed up the drying process again.
GE Dryer overheats
To prevent the dryer from overheating, verify that the heating element is not shorted out.
To test the continuity of the heating element, use a multimeter to check for continuity across the leads connected to each terminal, then check for continuity between each terminal and case.
If tested for continuity to case and is not present, replace the heating element and measure with a multimeter in which terminal or terminals are open when you move them (one at a time) from the full left position to the one notch off position.
The GE dryer is making noise
The drive belt is a critical component of your dryer. The drive belt wraps around the drum and pulley before connecting to the motor.
Much like the rest of your dryer, over time this belt can become frayed or otherwise damaged.
If you notice any signs of wearing or tear with your drive belt, inspect it for damage, if you see that the belt is damaged in any way replace it right away so that you don’t cause further damage to other nearby components.
GE Dryers take too long
Blower wheels work with the motor to draw air into the drum. Or, they can get clogged and lint can escape the filter and block airflow. The blower wheel also wears over time and can wobble.
If the airflow is weak, inspect the blower wheel for obstructions. If no obstructions are present and wobbling persists, replace it.
The GE dryer tripped the breakers
Circuit breakers can weaken over time. Even when the amperage draw is below the limit, a weak circuit breaker may trip too often.
Consider replacing the circuit breaker if you have checked all electrical components to the best of your ability and wish to avoid further expenses of a wiring inspection and repair.
The GE Dryer won’t shut off
The electric clothes dryer uses a heating element to warm up air to prepare it for the dryer drum. If this element fails, then the clothes will be far less dry compared to if they were working correctly.
Using a multimeter and checking for continuity (touching one end of the metering prong against the wire then touching another against each of the two terminal pieces on either side) you can test whether or not your heating element is faulty.
GE dryer troubleshooting
Related Guides
A red light came on that says “Low Air”
I cannot find anything about that in the manual.