Speed queen dryer troubleshooting. Few things are more challenging than finding your clothes wet after placing them in a dryer. If you’ve noticed that your clothes aren’t drying as usual and they come out damp, you’re probably wondering why.
There could be many reasons for an electric or gas dryer not heating up correctly but these reasons typically fall under two main categories: mechanical issues and electrical problems.
Some common mechanical problems include clogs in the vents of the dryer, faulty pressure switches, and malfunctioning fuses leading to no gas flow into the dryer itself. Electrical problems often arise because of damaged heaters or burned coils all of which can be replaced if need be.
Speed queen dryer troubleshooting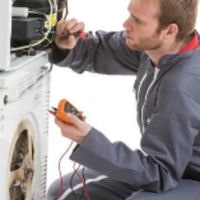
Check out this guide to see some suggestions on how to troubleshoot simple problems with your Speed queen dryer before calling a professional repairman. You’ll find that some of these basic fixes may do what is required to solve problems with your dryer.
The dryer will not heat up
The thermal fuse is like a safety blanket that protects your clothes dryer from overheating. The fuse is located on top of the blower housing or at the source of heat such as within the heating elements for electric dryers and gas burners for gas models.
When it is good, you will find that it has continuity when tested with a multimeter, meaning that there should always be an uninterrupted electrical circuit.
If it has been burned out, it won’t have continuity and needs replacement unless you want to fix whatever’s causing your dryer to overheat in order for it not to happen again.
It’s important that you always check your dryer venting when replacing this system because a restricted exhaust vent could cause another thermal fuse to blow too if they both go out – which would lead to more problems.
The Dryer won’t start
If your dryer isn’t running, the start switch might be to blame. If the dryer hums but won’t start, test the switch by trying to manually depress it in and out a few times, then trying to start the dryer again.
If there’s no change and you get no response from your dryer, go ahead and replace the start switch with a new one. If, on the other hand, you hear nothing or get no response whatsoever when you push down on the start switch, try testing the switch with a multimeter.
A good way to do this is to depress it in and out a few times while using your multimeter in continuity mode (one probe pressed firmly against one part of terminal C or R and one probe touching those same terminals at another point).
The Dryer takes too long to dry
Improper venting through a dryer will increase the upper-air drying time and will reduce the overall efficiency of both the machine itself and the adjacent ventilation ductwork.
The best method of testing this is to remove your dryer’s lint filter cap and then fan a piece of tissue paper back-and-forth over the opening.
If there are small portions of lint on the paper, you know that you have a clogged vent. If these “lint strings” cover most or all of your tissue sample, then your vent is 100% blocked.
The dryer has stopped spinning
The drive belt is a slender, long belt that wraps around the dryer drum as well as around two pulleys, including the tension pulley and the drive motor pulley. If it breaks from normal use over time, the dryer won’t turn on.
There are several ways to tell if your belt is broken one way is to reach into the dryer and manually turn the drum – since if it turns without any resistance, then it’s likely that you have suffered a damaged or broken belt.
Another approach would be to inspect the belt itself and see if there are any signs of wear and tear. Multi-colored belts indicate that they may be worn out; with stretched-out areas in between its grooves being another potential strong indicator of damage.
In both these instances, it’s safest to replace your old drive belt with a new one; however, there is further information below for those who might feel confident about performing repairs on their own clothes dryers.
The dryer makes noise
One or more of the dryers may have worn-out rollers. Dryer rollers are drum-shaped structures that help to keep the clothes tumbling in a steady circle. Over time, their bearings can wear thin, making for a loud and sometimes irritating noise when spinning.
If this is the case, you need to figure out where the noise is coming from and make sure the cause isn’t something more serious than just worn parts like joints or metal fatigue.
The dryer is overheating
A heating element is an electromagnetic device that heats up when connected to a power source and starts emitting heat. The heating element’s primary function is to supply heat inside clothes dryers.
In the event that the heating element breaks, it could cause many problems ranging from A faulty drying cycle, damage in electronic control units, corrosion of electrical contacts, and malfunctioning appliance wiring components.
Next, test the continuity of the thermostat by using a multimeter. When the thermostat does not have continuity, replace the thermostat.
The dryer drum is not turning
Dryers have rollers that support the interior drum, allowing it to spin freely without strain on your washer and dryer. Occasionally these rollers will develop problems such as becoming loose or worn out, and you may need to replace your roller assembly.
This can happen at any point during the life of a dryer leading to sometimes unexpected breakdowns when they could have easily been avoided by making minor replacement parts upgrades soon after being made aware of potential issues due to wear and tear or fraying.
Related Guides